Mission
Artists & Artisans
stretching gold to an extreme thinness of 1/10,000mm.
The trick of the trade, stretching gold to an extreme thinness, and the paper loading process said to be a determining factor in gold leaf production. Gold leaf is made by tirelessly beating out and stretching alloy of pure gold with minuscule traces of silver and copper. An alloy about the size of a 10 yen coin becomes the size of one tatami mat with a thickness of 1-1.2/10,000 millimeters, This is so thin that light appears to penetrate right through it, and when you touch it with your fingertip, it cups and adheres closely to the skin, turns into a delicate powder, and vanishes. Being such a fragile material, you cannot afford to lose focus for an instant in the foil beating process. Since it is prone to becoming charged with static electricity, thin sheets of alloy are sandwiched by thin sheets of paper one sheet at a time, beat and stretched, gradually becoming thinner and thinner after undergoing a multi-stage process before being completed. Foil beating requires that the luster inherent in gold is kept as the gold is stretched out to a uniform thinness, and this is where the high level techniques of the artisan shine. The process of beating and stretching out the alloy over a long stretch of time calls for tremendous perseverance and physical strength.
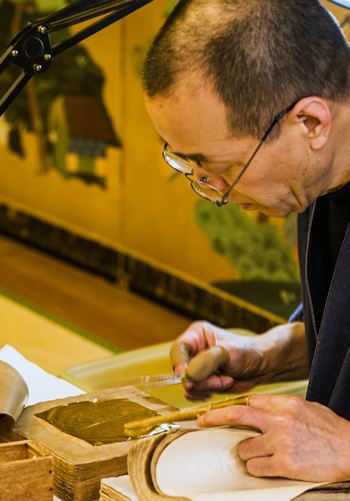
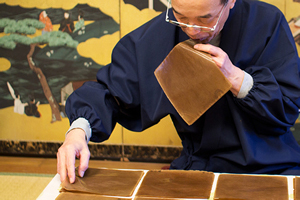
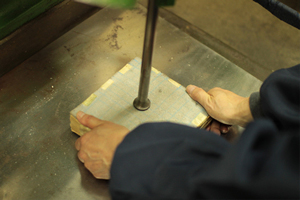
tradition passed down, the delicate and complex art of gilding
Delicate gold leaf is so thin that it vanishes with a simple touch. Gilding is done using bamboo chopsticks to prevent static electricity. Gaps are unacceptable, yet too much overlap ruins the gold leaf. It is a spectacle to see the skill of placing foil on an object while maintaining a constant speed and steadily adjusting the seams between sheets, even with items of complex shape, all the while envisioning the final form. Tradition thrives in a variety of processes and techniques. Gold leaf — crafted by artisans at the cost of many hours and a good deal of work on the part of the artisan — is used widely from craft products to food products, morphing its appearance and becoming something that is familiar to everyone.
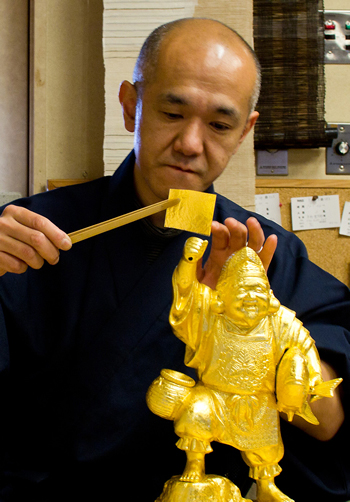
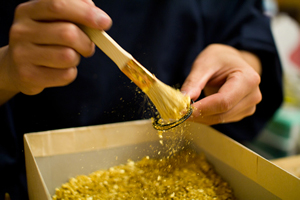
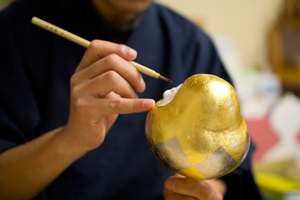
Kaga maki-e (lacquer art) got its start when the third generation clan leader of the Kaga clan, Toshitsune Maeda, invited renowned master craftsmen such as Igarashi Doho and Kiyomizu Kyubee from Edo and Kyoto. Its distinguishing characteristic was a stately and vibrant decorative technique dubbed Kaga maki-e.
It is an eye-opener to see the highly-developed skill of sprinkling gold and silver powder on lacquer (maki-e, “sprinkling picture”), which acts as an adhesive, inlaying seashells (raden inlay),
creating a white color with egg shells (rankaku egg-shelling), and the method of raising up the design.
・Kaga Maki-e Artist
Nakamura Tadashi (Artist Name: Tadashi)
After undergoing official maki-e training in Kyoto and Kanazawa for several years, Tadashi built up his craft making maki-e for tea ceremony goods, Buddhist altars, and writing equipment, becoming a maki-e artist that expresses the subtlety and grace of Kaga maki-e. He has participated actively in private and art exhibitions and has repeatedly placed his heartfelt efforts into pursuing the possibilities held by maki-e and himself, leading up to where he is now.
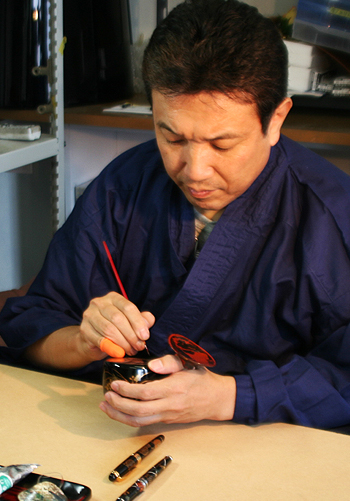
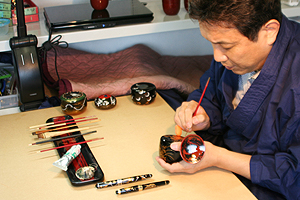
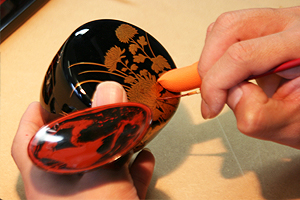
The Gold Leaf Manufacturing Process
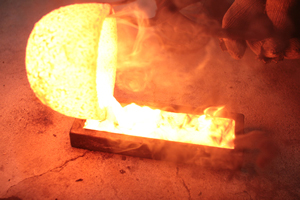
Gold bullion and trace amounts of silver and copper ingot are melted at high temperatures of around 1,300°C in a melting furnace, poured into a mold, making molded gold alloy. Up to 4kg can be melted in oven bowls.
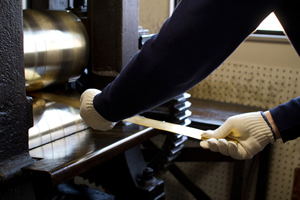
The molded alloy is rolled into strips of 6cm wide and approximately 5/100mm thick in a rolling mill.
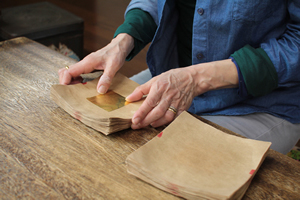
The rolled ribbons cut into 6cm pieces are called kopei, or small sheets. Approximately 200 sheets of kopei are placed between clearing paper one sheet at a time, wrapped in bag leather, and stretched out in beating machine. The stretched gold is gradually moved into larger paper five times, forming an upper clear square approximately 20cm across and 2/1000mm thick.
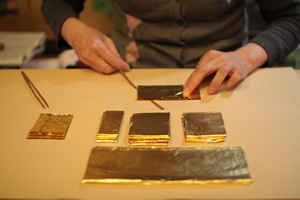
The 20cm upper clear square is cut into approximately 12 equal portions. The items cut into small pieces are called koma
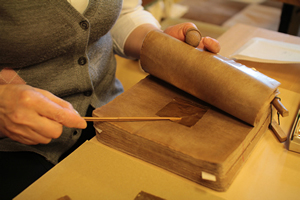
The koma are placed in between prepped beating paper, and wrapped in bag leather with approximately 1,800 sheets making up one pack.
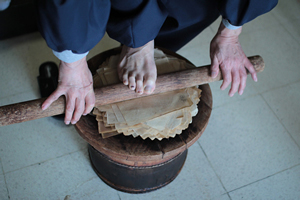
The raw paper used as beating paper (gampi paper) is soaked in a mixture of straw ash, persimmon juice, and egg whites, then wrung out.
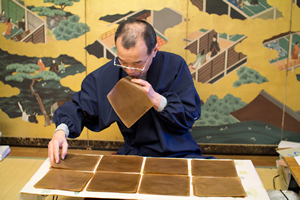
The paper that has been wrung out is repeatedly beaten in a machine made exclusively for paper prepping, taking approximately three months to evolve into beating paper. The success or failure of the foil prepping process has a significant influence on the quality of the gold leaf, making this an important task.
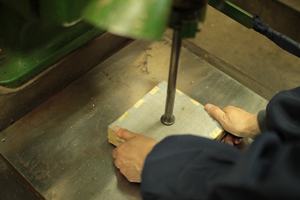
The packs wrapped in bag leather are beat for roughly three minutes in a foil beating machine that moves up and down 700 times per minute, cooled off for 15 minutes, and the process is repeated dozens of time until the pack is beat and stretched out to a thickness of roughly 1-1.2/10,000mm.
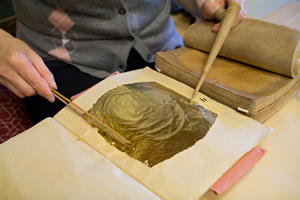
The beaten gold leaf is extracted out onto a wide pad.
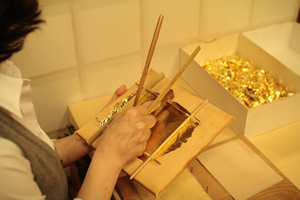
The gold leaf extracted out onto the wide pad is placed on top of a leather board and cut one-by-one into the standard size of 109mm squares with a bamboo frame, which are placed between handmade interleaf paper and finished in units of 100 sheets.
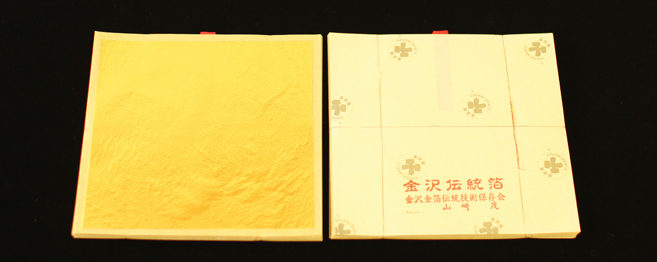